The Key to High-Quality Plywood: Veneer Drying Techniques
The Key to High-Quality Plywood: Veneer Drying Techniques
Introduction:
Veneer drying plays a crucial role in the production of high-quality plywood. As the foundation of this versatile material, properly dried veneer ensures stability, strength, and durability. In this article, we will explore the various techniques used in veneer drying and their significance in the plywood manufacturing process.
1. Veneer Dryer: A Game-Changer in Plywood Production
The veneer dryer is a revolutionary piece of equipment that has transformed the plywood manufacturing industry. With its efficient and controlled drying capabilities, it ensures the veneer's moisture content is reduced to the optimal level, preventing warping, cracking, and other defects.
2. Veneer Roller Dryer: A Versatile Drying Option
One widely used technique in veneer drying is the veneer roller dryer. This method involves passing the veneer through a series of heated rollers, which gradually remove moisture from the wood. The controlled pressure and temperature in this process ensure uniform drying and minimize the risk of damage to the veneer.
3. Mesh Veneer Dryer: Ensuring Consistency and Quality
Another popular technique is the mesh veneer dryer. In this method, the veneer is placed on a mesh conveyor belt and subjected to hot air circulation. The mesh allows for even distribution of heat, ensuring consistent drying throughout the veneer. This technique is particularly effective for thin veneers, as it minimizes the risk of warping or distortion.
4. Importance of Proper Veneer Drying
Properly dried veneer is essential for the production of high-quality plywood. It not only enhances the plywood's structural integrity but also reduces the risk of defects such as delamination and dimensional instability. Additionally, well-dried veneer allows for better glue adhesion, resulting in a stronger bond between the layers of plywood.
5. Factors Affecting Veneer Drying
Several factors influence the veneer drying process, including the species of wood, initial moisture content, drying temperature, and airflow. Each wood species has unique characteristics that require specific drying conditions to achieve optimal results. Additionally, controlling these factors helps prevent over-drying or under-drying, ensuring the veneer retains its desired properties.
6. Quality Control in Veneer Drying
To ensure the highest quality plywood, manufacturers implement stringent quality control measures during the veneer drying process. Regular moisture content testing, visual inspections, and adherence to industry standards are essential to identify and rectify any issues promptly. This attention to detail guarantees that only the finest veneer is used in plywood production.
Conclusion:
Veneer drying is a critical step in the manufacturing of plywood. By employing advanced techniques such as veneer roller dryers and mesh veneer dryers, manufacturers can achieve consistent and high-quality results. Properly dried veneer enhances the structural integrity of plywood, reduces defects, and ensures a strong bond between layers. With meticulous quality control measures in place, the veneer drying process paves the way for exceptional plywood products that meet the demands of various industries.
Contact us :
Whataspp/Telegram: +8618769900191 +8615589105786 +8615805493072
Email: minghungmachinery@gmail.com
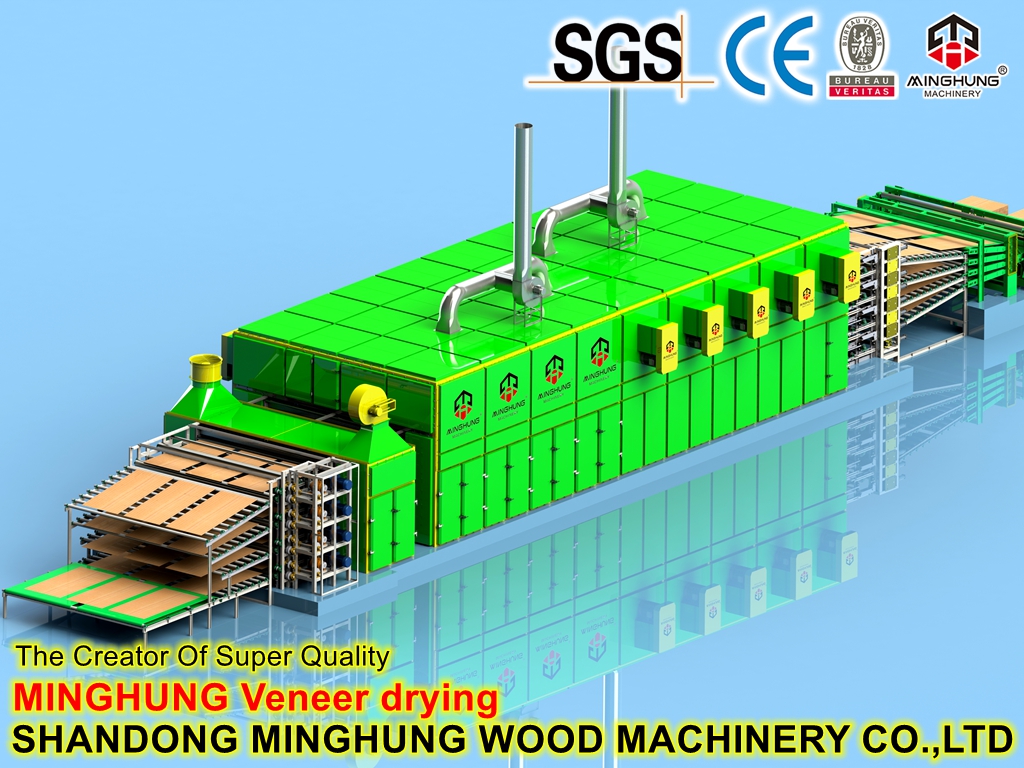
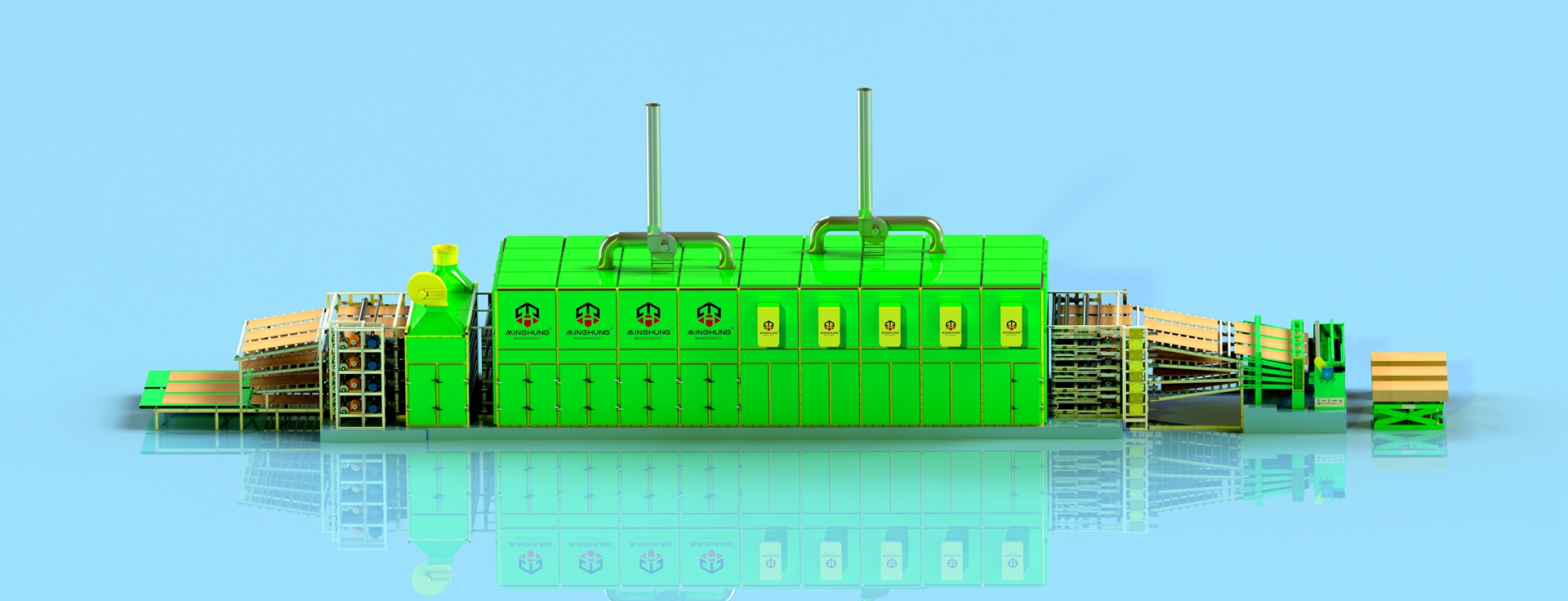
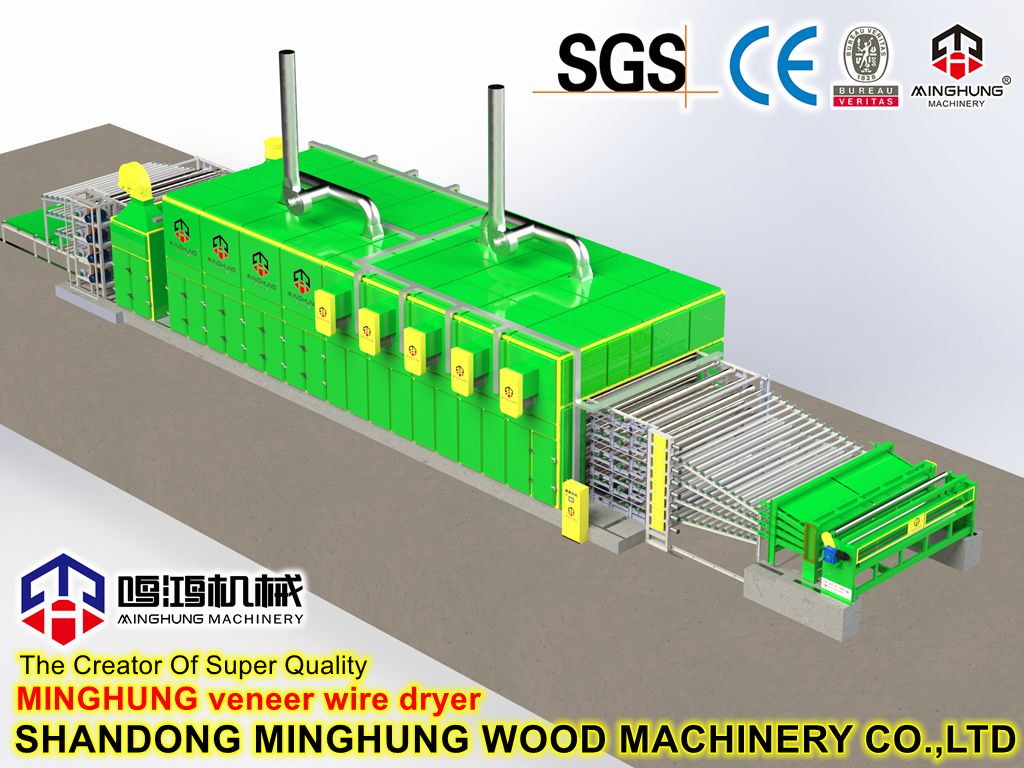
MINGHUNG veneer dryer adopts stainless steel 30 mesh bag + roller to ensure the flatness of veneer. The working width of the machine is 2.8 meters, with four layers. Taking drying eucalyptus as an example, the thickness of eucalyptus veneer is 1.7mm, and the moisture content is 60-70%. The dryer works for 20 hours a day and can dry 90-120 cubic eucalyptus veneer. The remaining moisture of eucalyptus veneer is: %10--%14, the eucalyptus veneer after drying has a smooth and even moisture content. Because the mesh bag method is adopted, the problem of reducing the thickness of the veneer caused by roller extrusion is eliminated, and it is suitable for drying various veneer veneers.
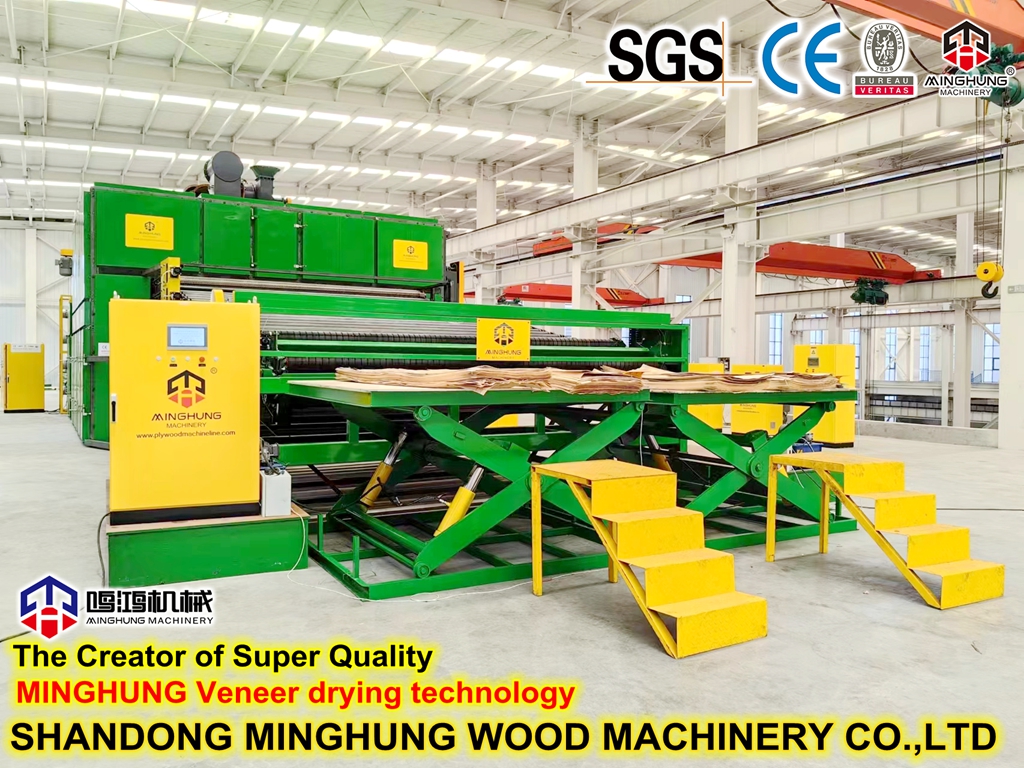
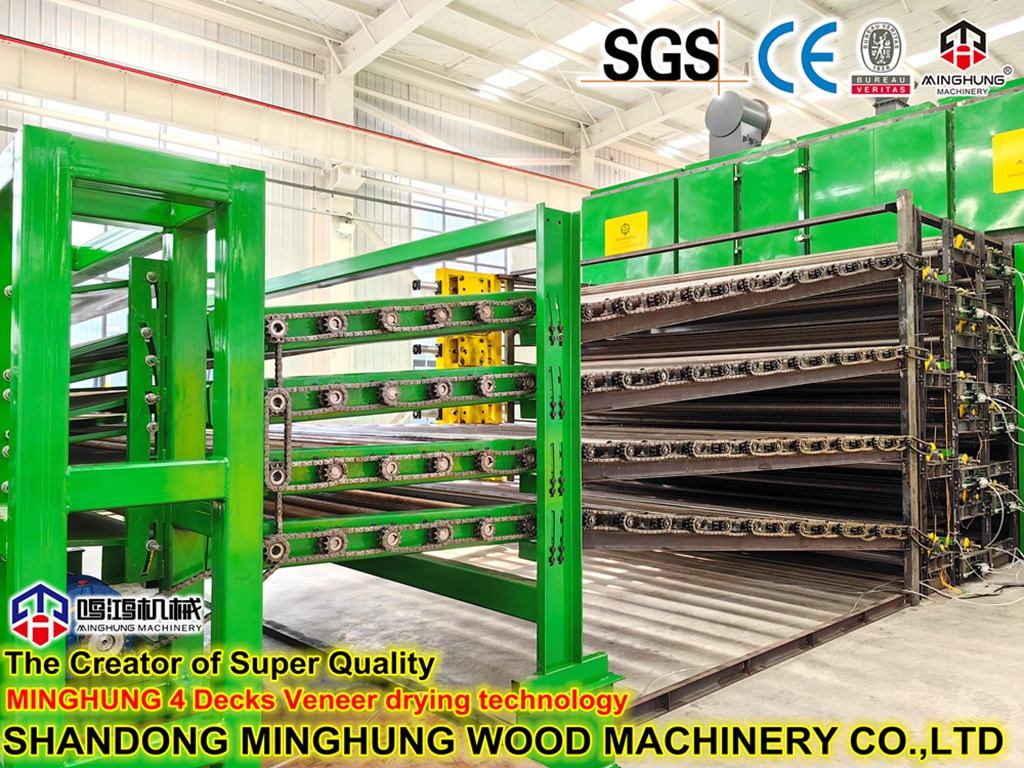
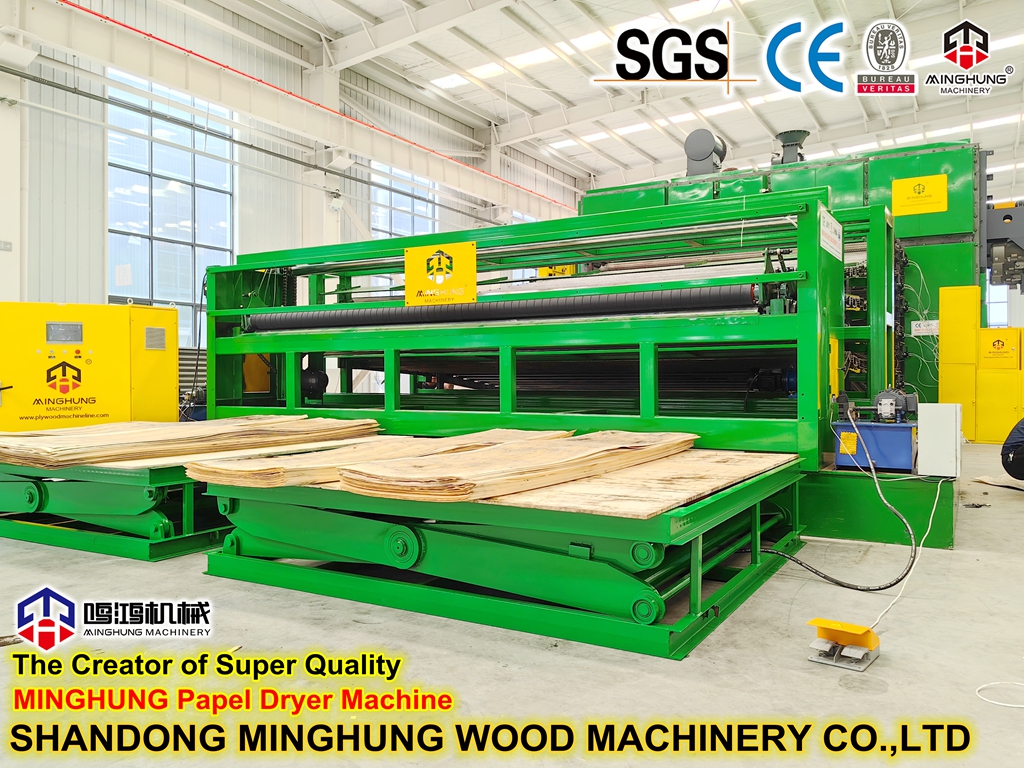
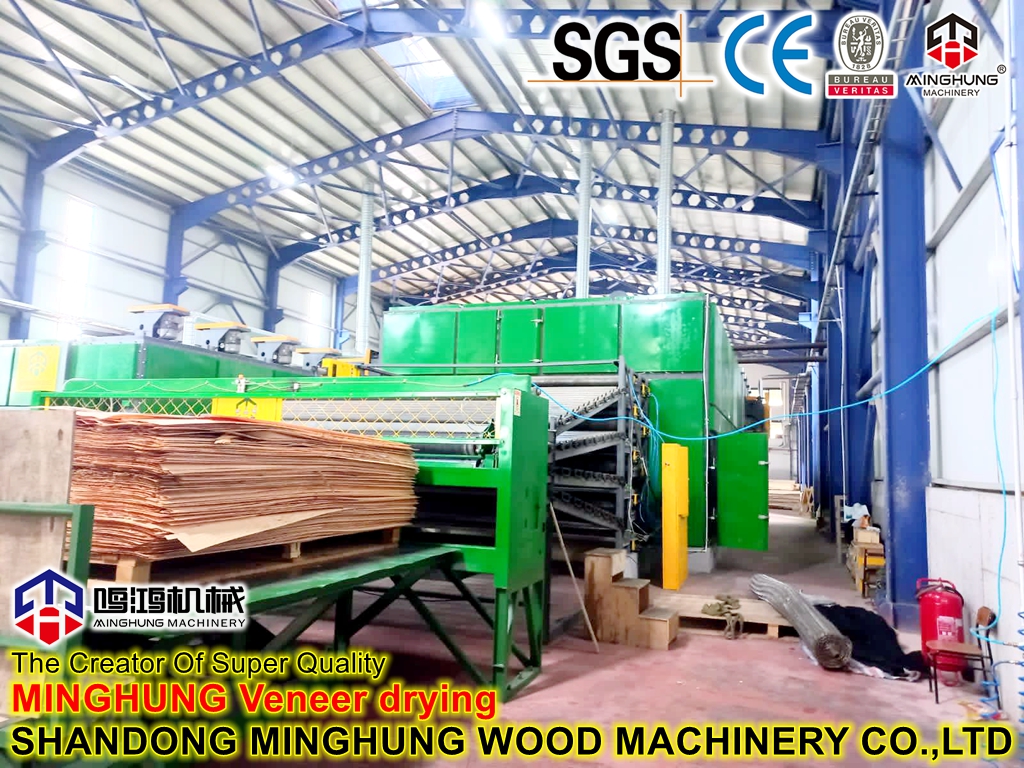
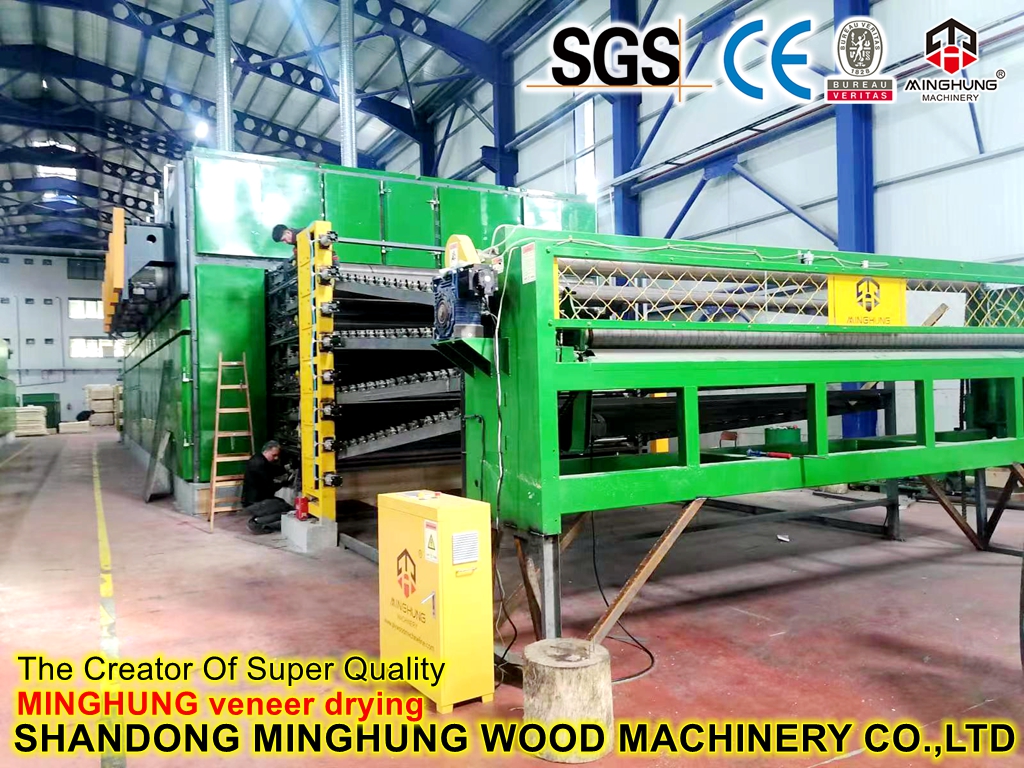
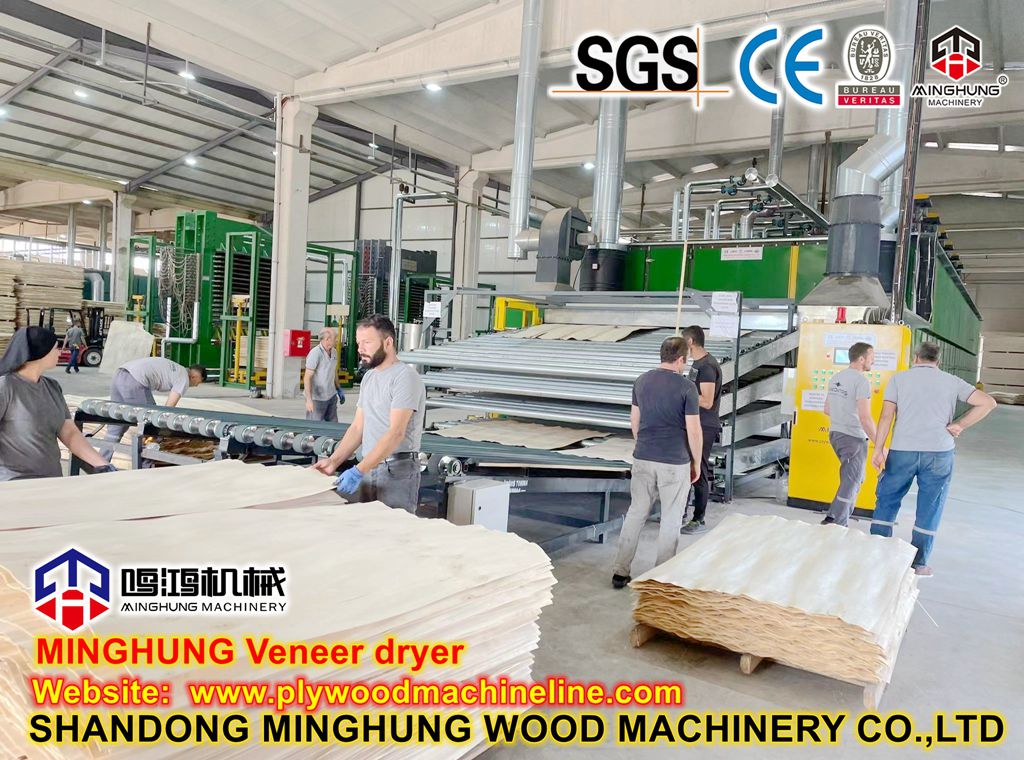
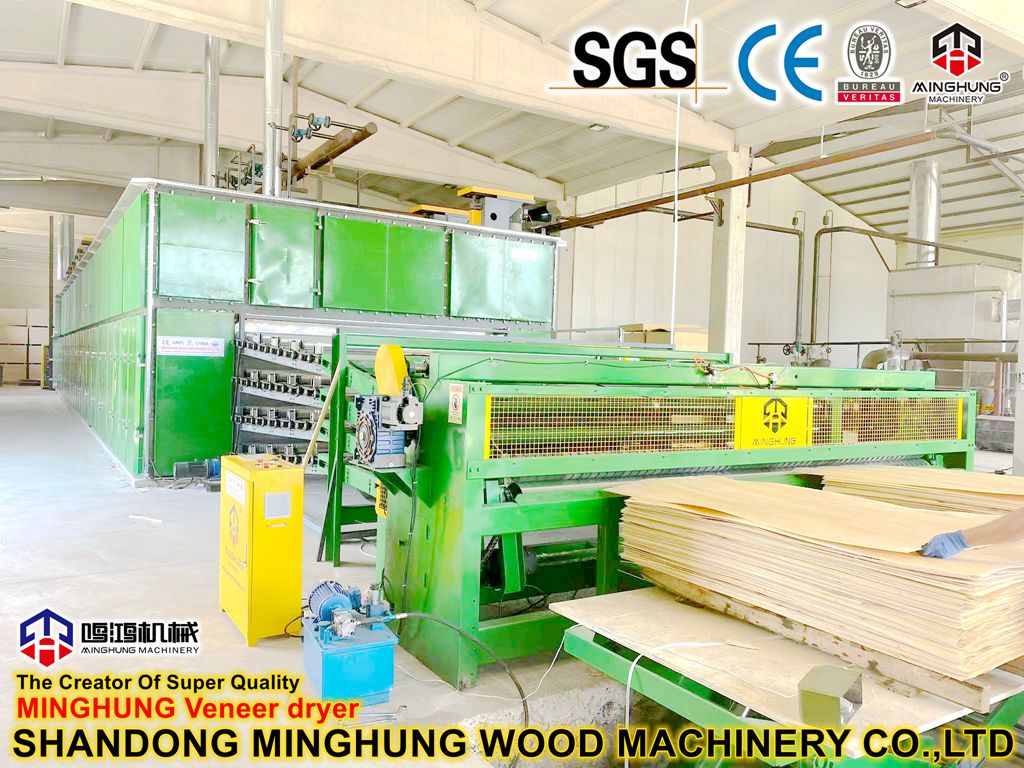
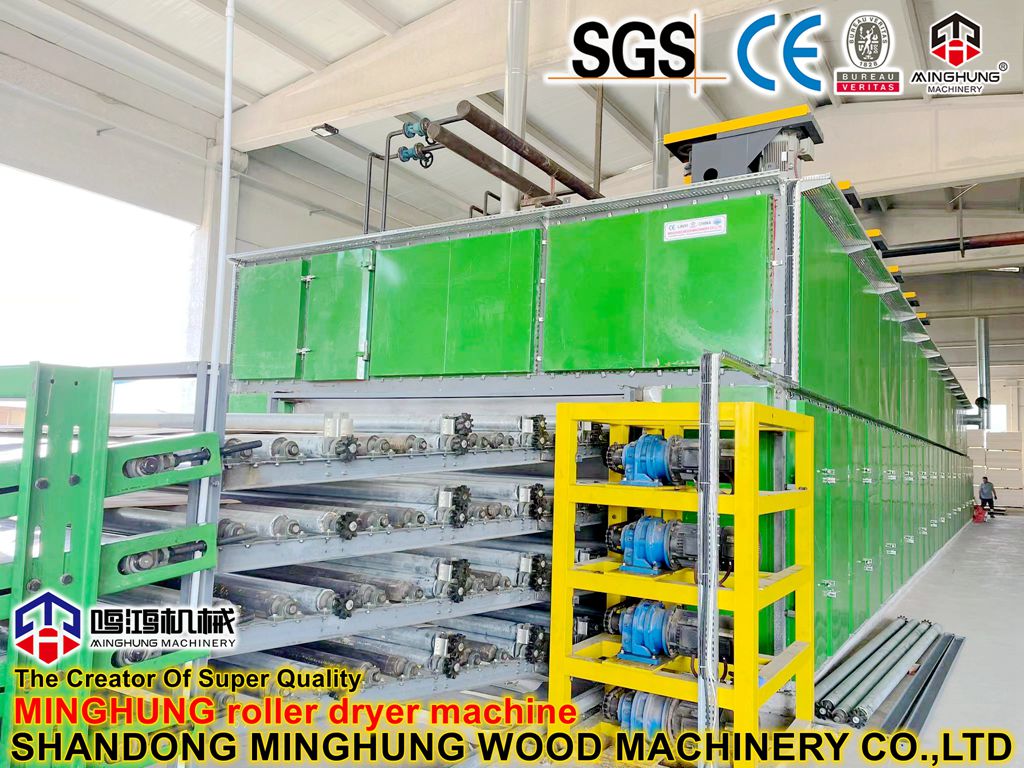
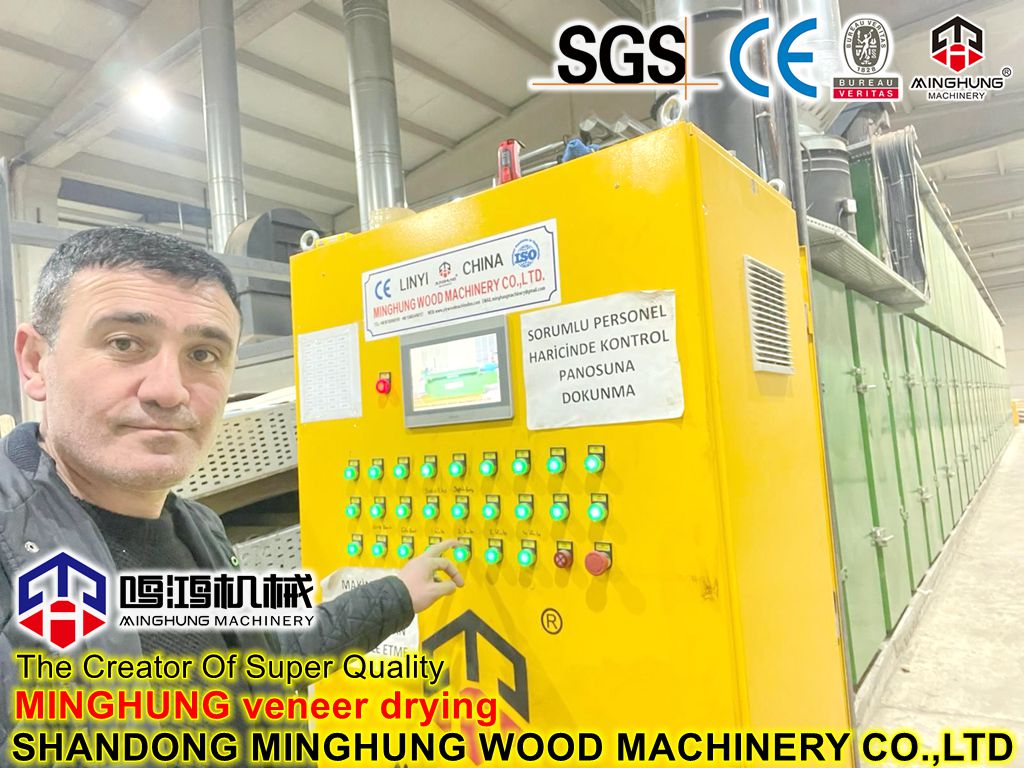
MINGHUNG veneer dryer is a dryer specially developed for traditional dryers with high energy consumption, low drying efficiency, uneven drying of veneers and high mechanical failure rate. This model has high energy consumption and high heat conversion rate. , The drying veneer is flat, the failure rate is low, and the pain point of the traditional dryer is solved. This model has the following advantages:
1. High output at low temperature, ensuring the flexibility and flexibility of the veneer, fast speed and large output. According to the needs of different users and different materials, the output of the equipment can reach 3-4 cubic meters per hour.
2. In order to achieve the flatness of the drum, we optimize the density of the internal machine structure to reduce the pressure, completely solve the problem of the flatness of the veneer, and avoid the problem of reducing the size of the veneer caused by excessive pressure. Smaller shrinkage than all dryers on the market, no loss of veneer,
3. High degree of automation, automatic feeding and labor saving, automatic dehumidification, low cost of consumables, high efficiency and energy saving, low power consumption, the equipment adopts all-aluminum fin heating device, large heat exchange area, fast heating, large circulating air volume, and many cycles. High thermal efficiency, drying equipment saves more than 40% energy. All cooling fins adopt forced circulation system to enhance fluid flow rate, improve heat exchange efficiency, and effectively reduce heat loss. At the same time, the problem of excessive wind resistance caused by high coil density is effectively solved, and the heat transfer process is improved by 1.5 times compared with the traditional dryer.
Good veneer dryer need good accessories
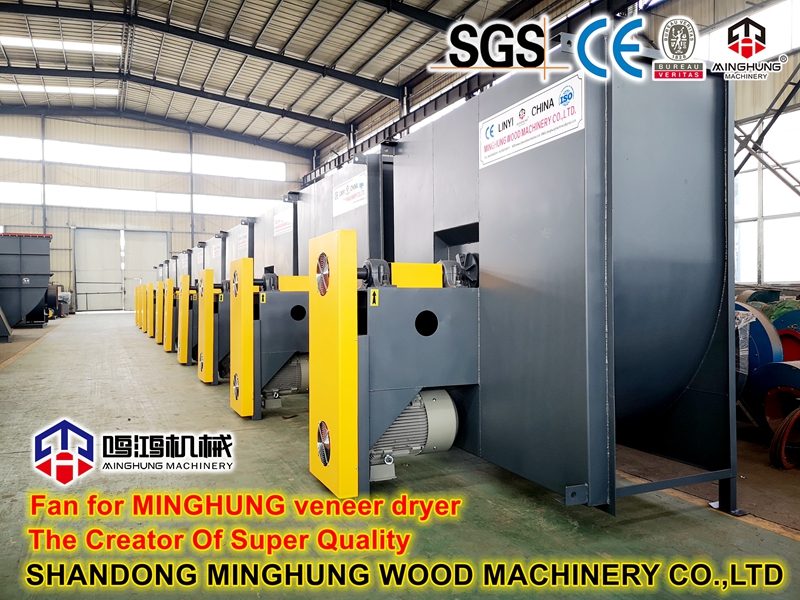
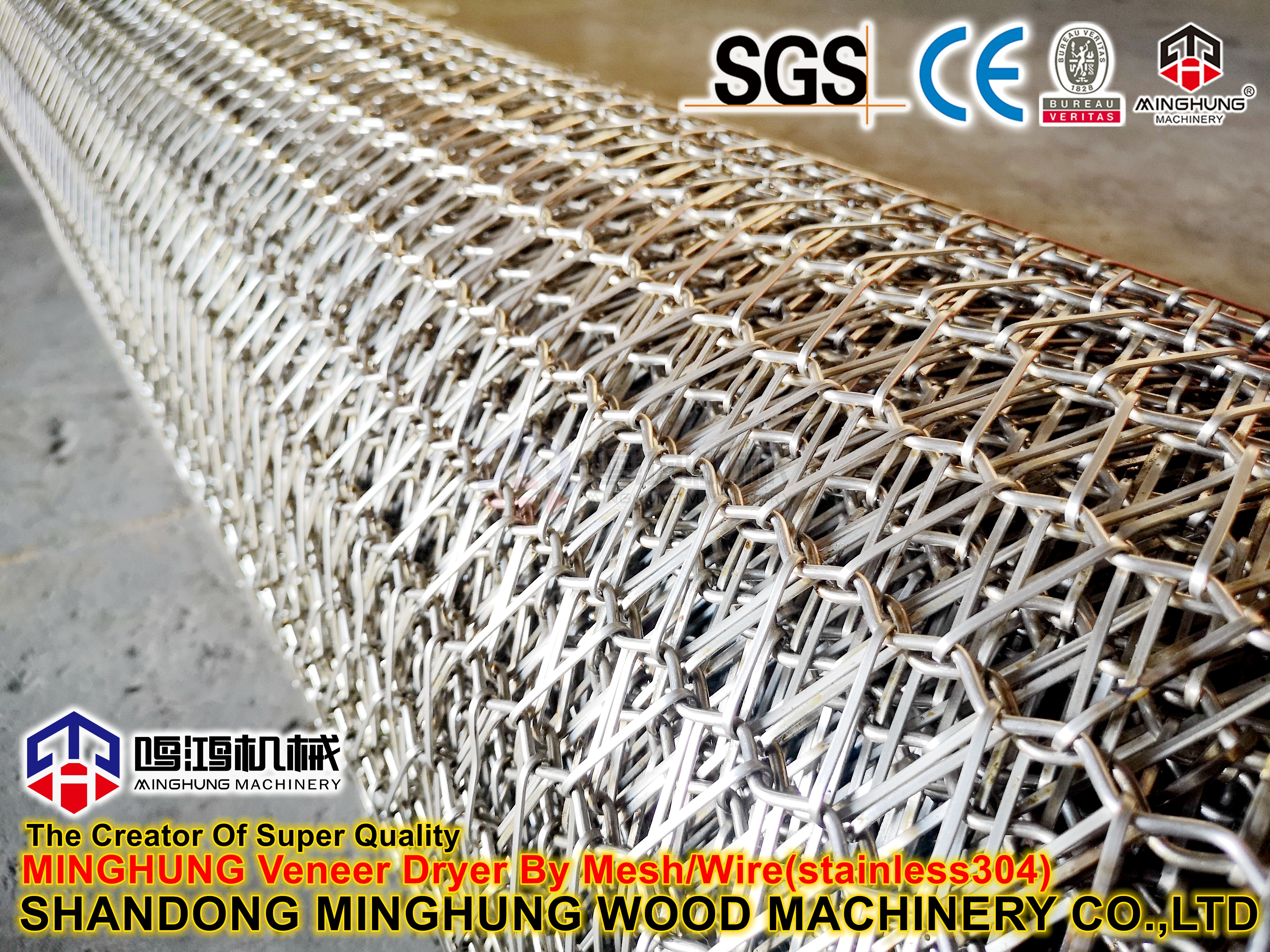
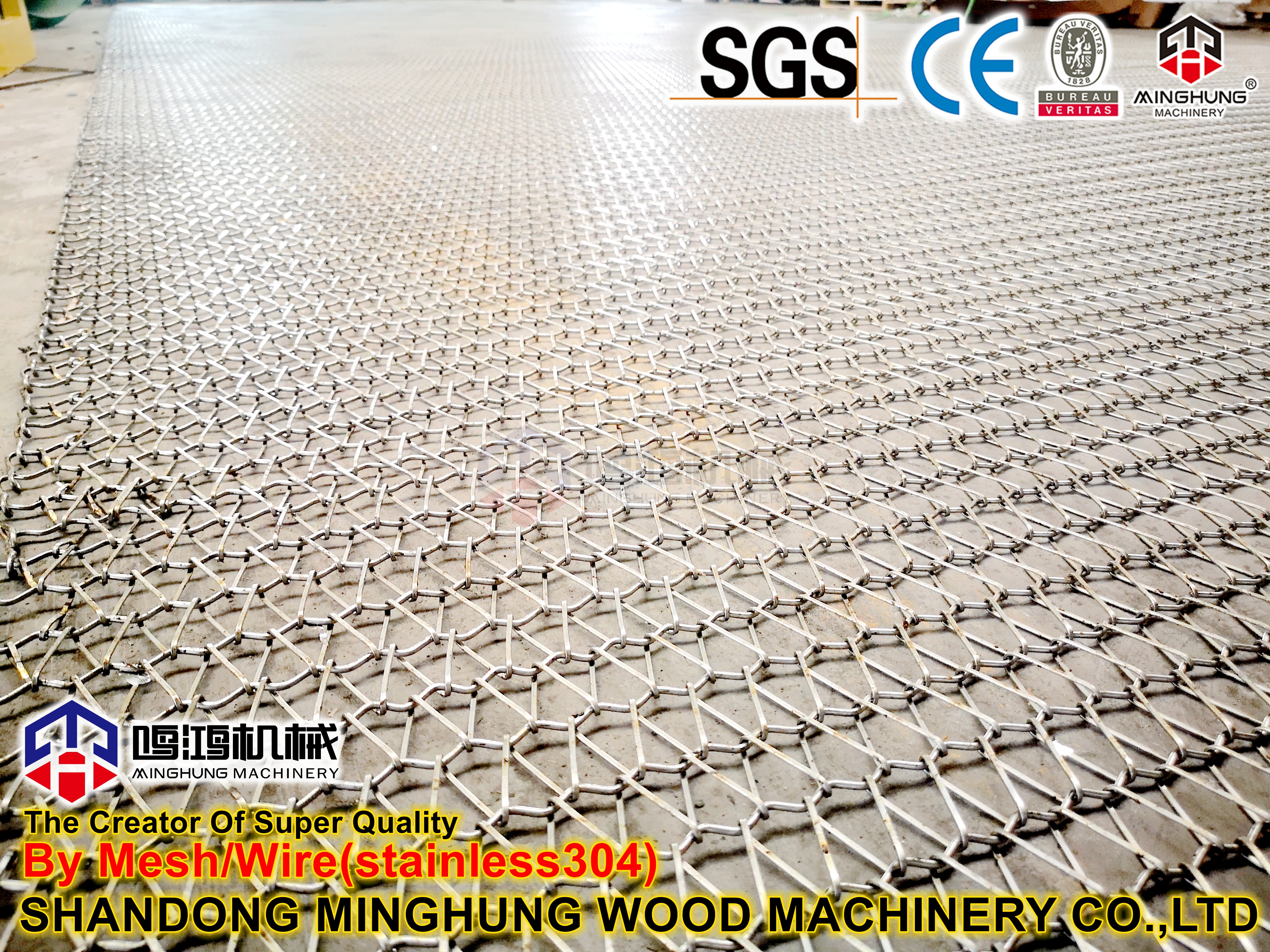
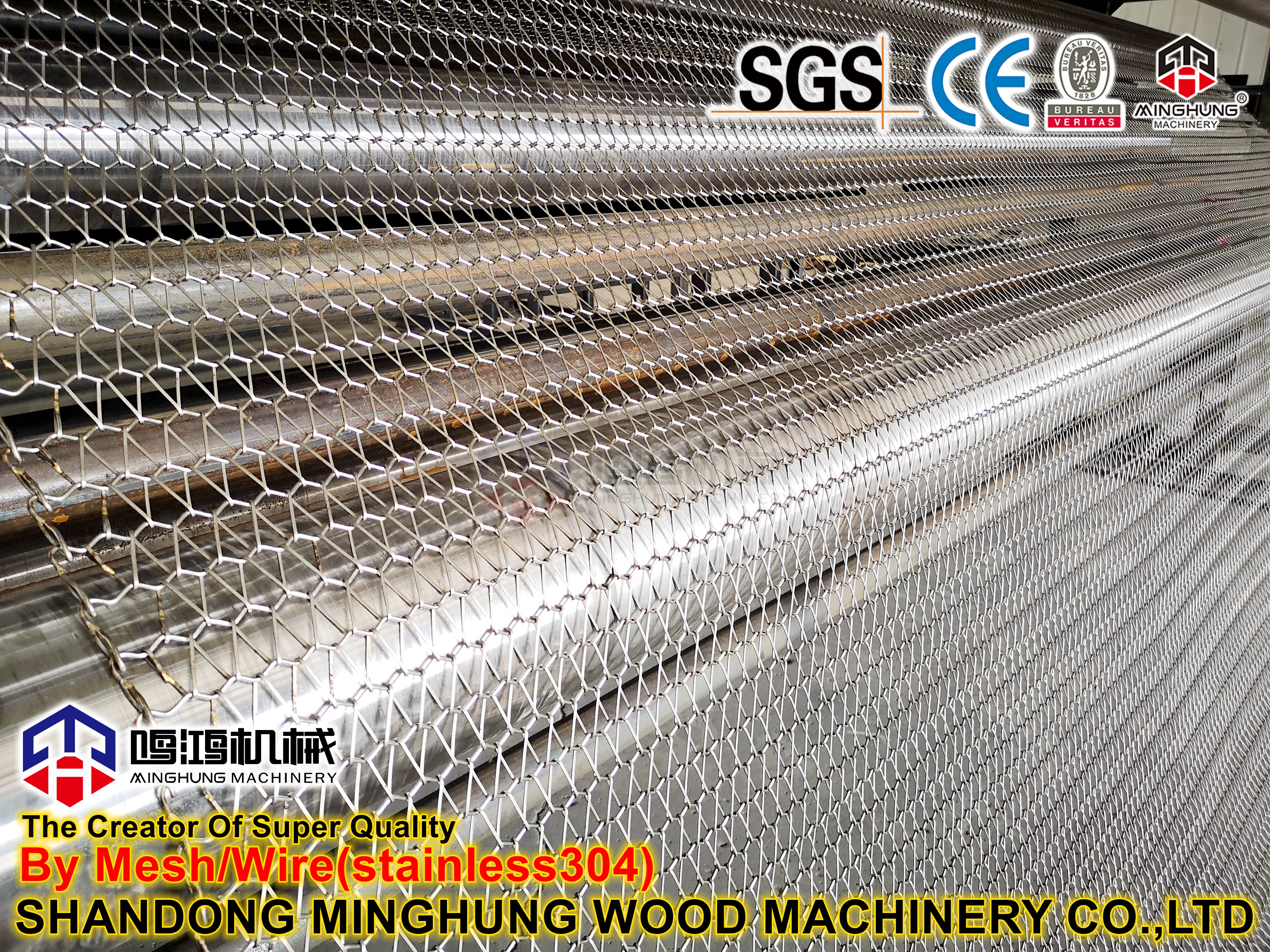
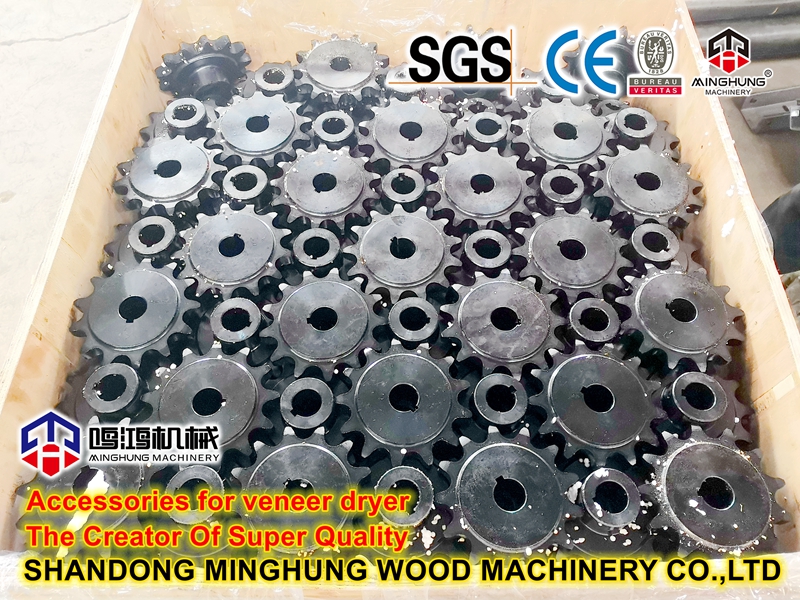
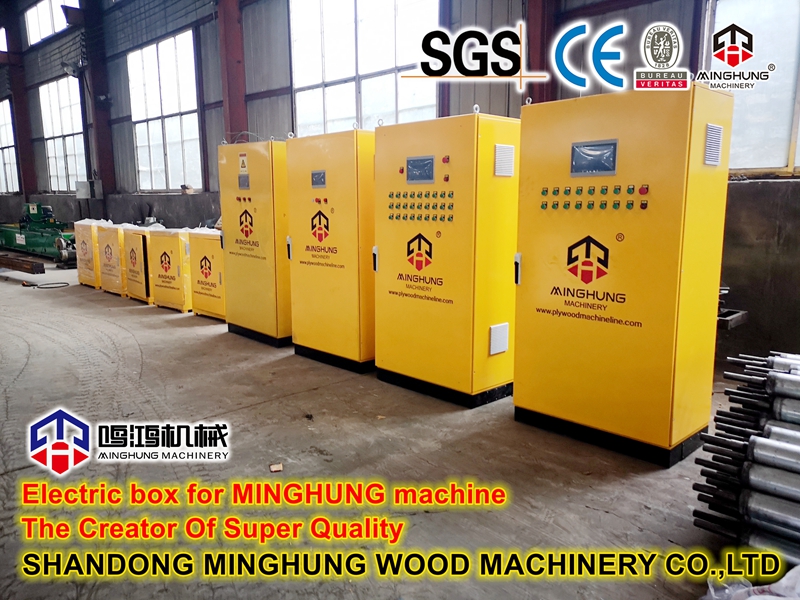
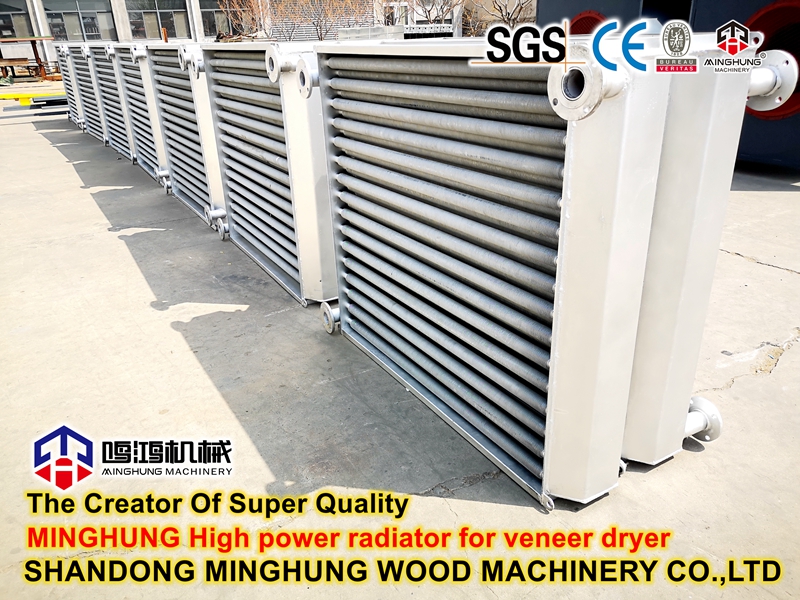
veneer dryer delivery:
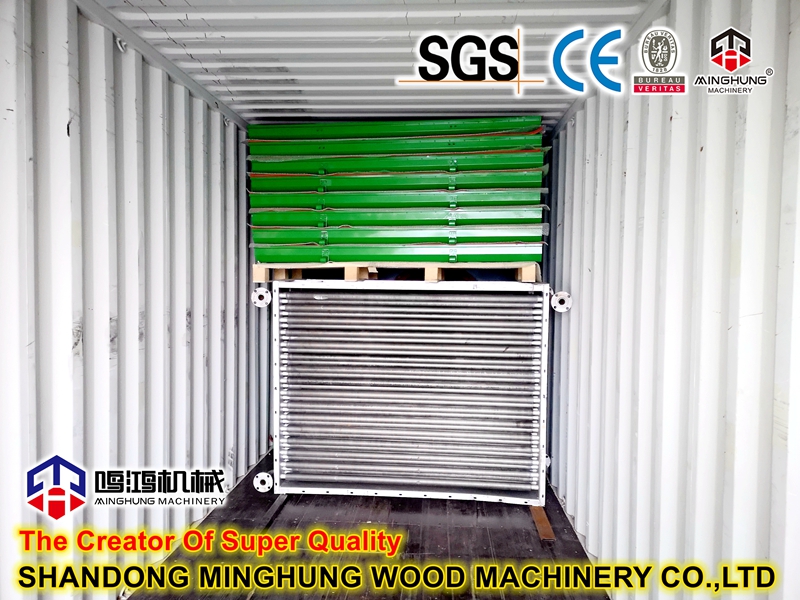
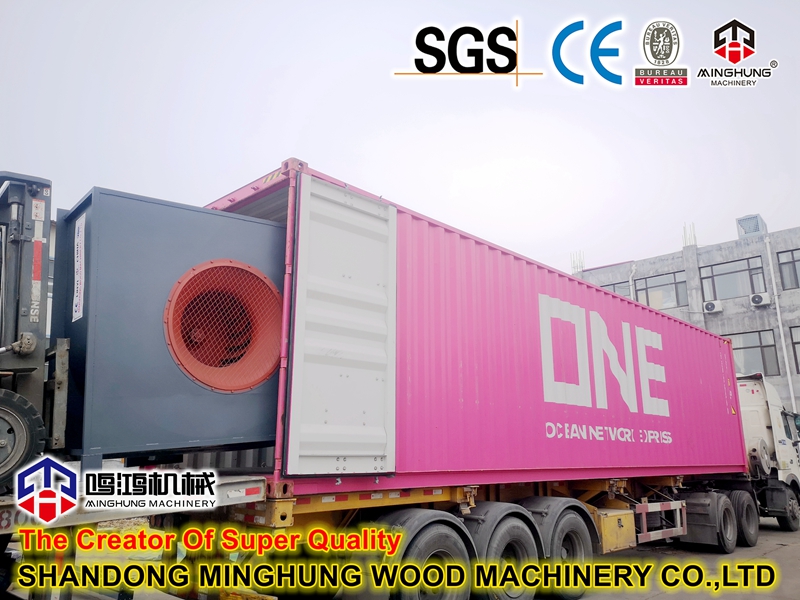
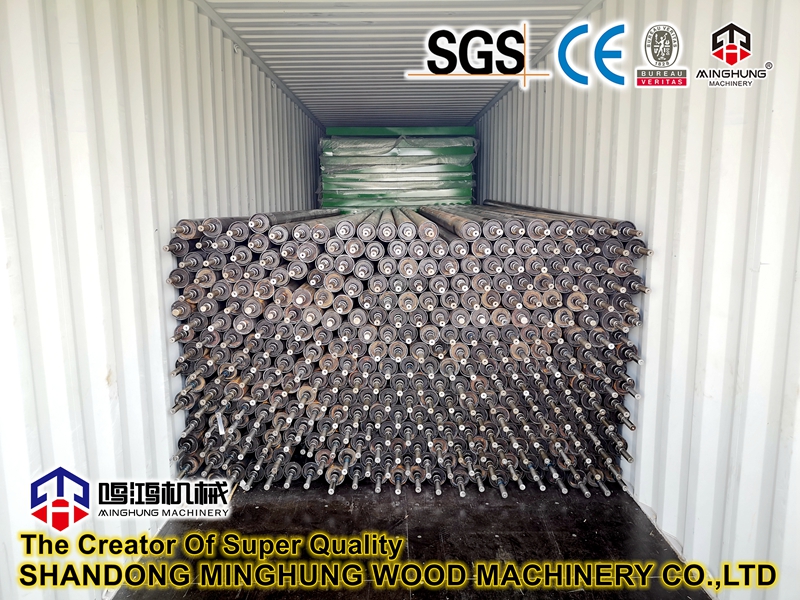
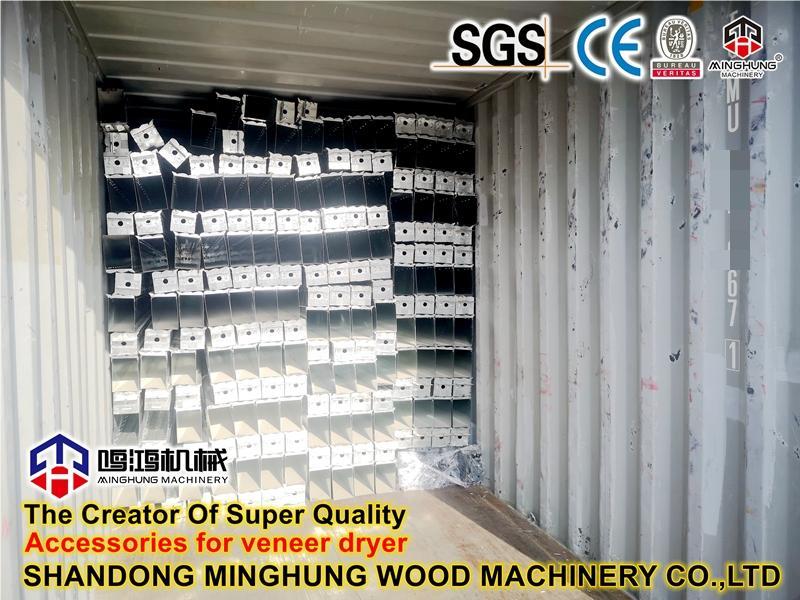
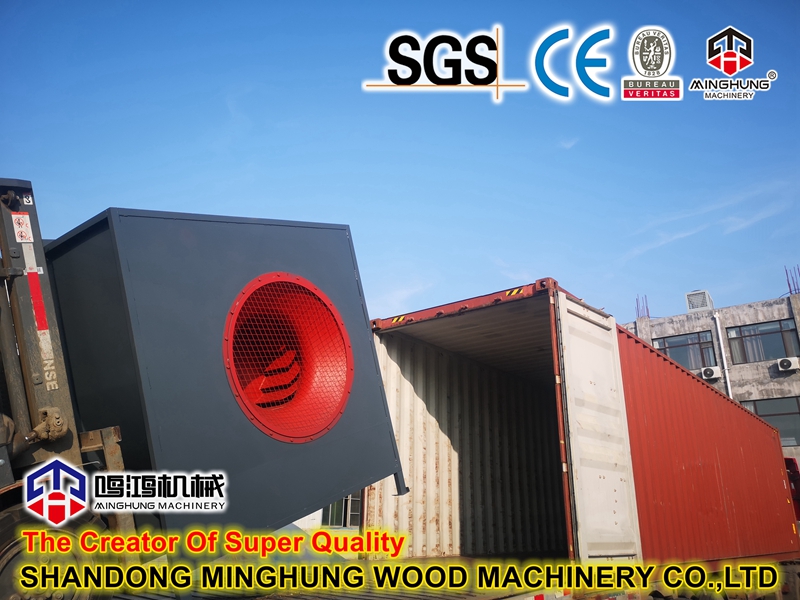
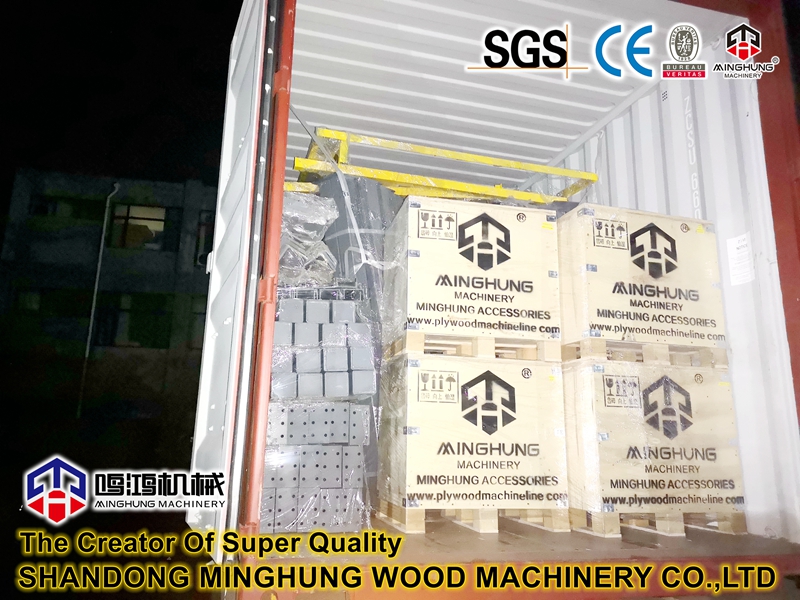
Contact us :
Whataspp/Telegram: +8618769900191 +8615589105786 +8615805493072
Email: minghungmachinery@gmail.com